Mission
FabuLens is a subsidiary of the Federal Agency for Disruptive Innovations SPRIN-D. In cooperation with mcd – modern camera designs GmbH, we are developing an innovative optical manufacturing technology – LENSCURE™ – which is based on UV-replication. This technology makes it possible to produce large numbers of high-precision optical polymer components in a cost- and energy-optimized manner.
Our aim is to revolutionize high-volume production of optical components and systems and establish the same in Germany and Europe.
The standard manufacturing process for such optics is currently the well-known precision optical injection molding. Polymers are melted at high temperatures, injected into the mold under high pressure and then cooled. This requires a large number of molding systems under clean room conditions and a great deal of energy. By converting the process to room temperature and parallelizing it much more we can use fewer machines and reduce energy consumption to up to five percent of the original value.
Our new process revolutionizes the manufacturing process for miniaturized, high-precision imaging optics. It combines the advantages of optical precision injection molding with the scaling possibilities of wafer-level optics known from semiconductor production.
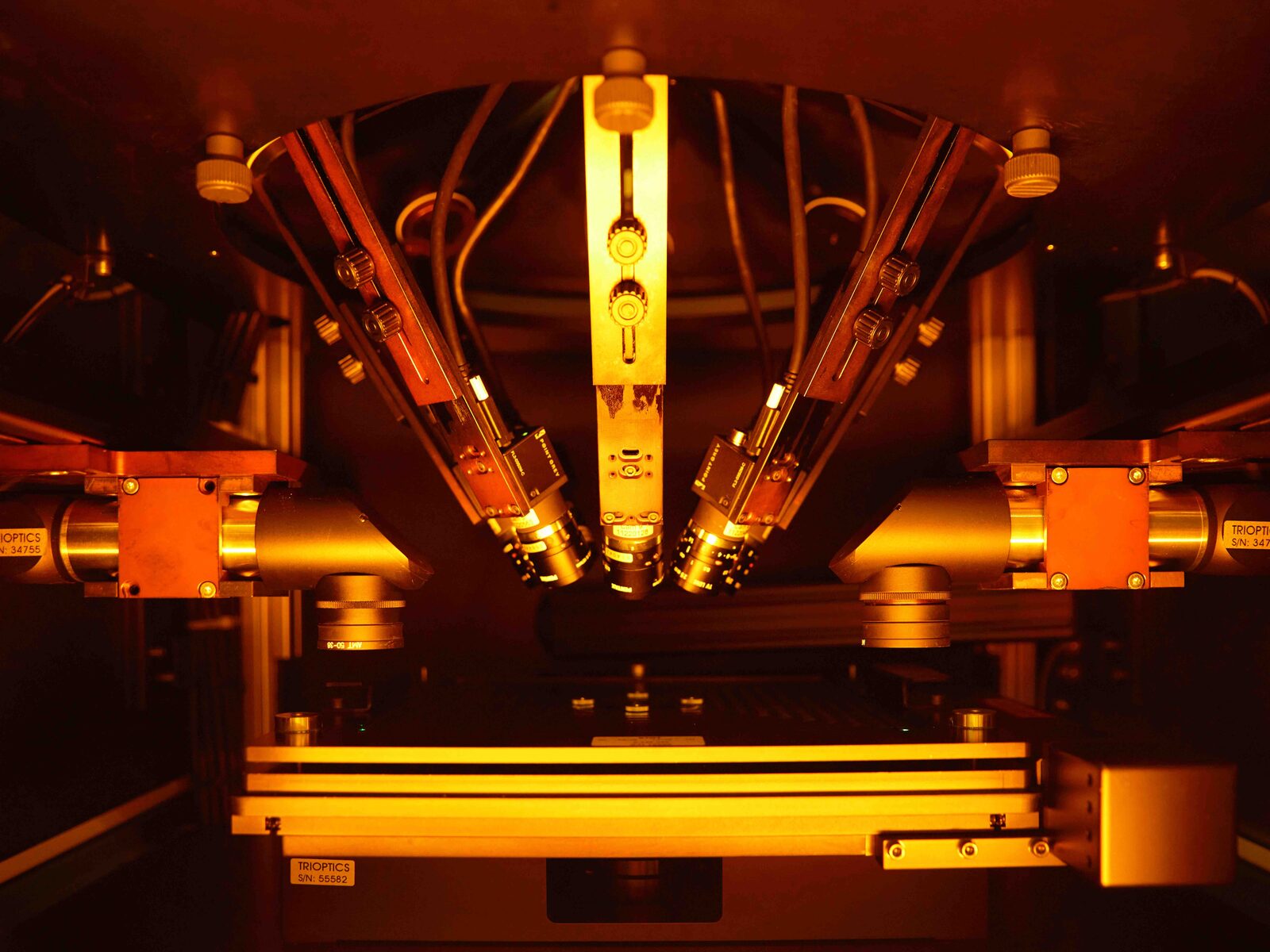
The idea
We have found a way to combine the advantages of the injection molding process with those of wafer-level optics – without compromising on optical performance.
We rely on an UV-replication technology that allows to produce up to a thousand aspherical, monolithic polymer lenses with imaging quality in a single step. These can therefore be produced very cost-effectively and used in high-volume products.
On the other hand, low initial costs for tool origination enable the cost-effective production even of small quantities. This makes our technology an enabler: Innovative products that are initially only in small quantity demand, e.g. in medical applications, can later also be produced in large quantities, still at at optimized costs..
WAFER-LEVEL OPTICS
- High-temperature polymers
- High parallelization (for production and integration)
OPTICAL PRECISION INJECTION MOLDING
- Any lens shape
- Many lens elements per objective lens possible
- Very high resolution
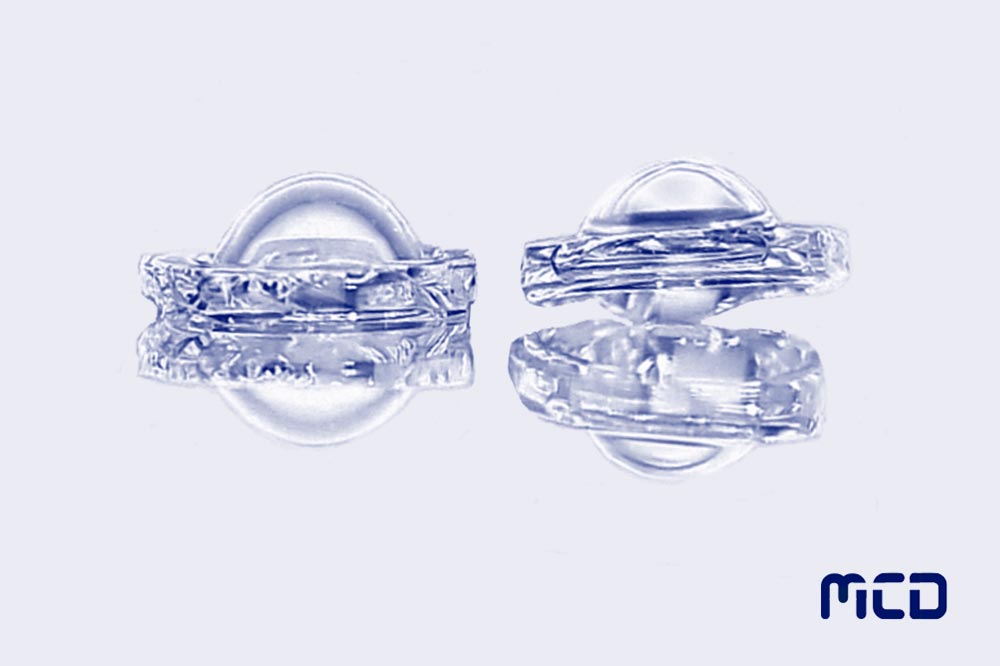
Our chances
HIGH-RESOLUTION IMAGING
Meniscus-shaped lenses
- No glass substrates in the optical path – ideal for high-res lens design
Minimal surface deviations for large vertex heights of the lenses and thus large diameters
- Shrinkage compensation
Aspherical lenseses
- Can take on almost any shape – ideal for correcting image errors at small F-numbers
Materials with different Abbe numbers for achromatization
- Crown and flint materials
Production at room temperature
- Simple equipment + inexpensive tools
- Low initial costs
- Cost-efficient even at small quantities
- Low energy consumption
Parallelized batch process
- Cost-efficient production of very large quantities
- Easily scalable production quantities
High-temperature stable optical polymers
- Can be used in applications that would otherwise not be possible with polymer optics due to critical temperature requirements
- Simplified integration of camera modules due to usability of reflow soldering processes

Cost advantage for small and large quantities.
Drastic reduction of energy consumption and CO2 emissions in the manufacturing process.